Zircaloys have anisotropic physical, mechanical, and chemical properties. Within the oxide layer, the alloying elements affect the atomic transport such that the alloying focus determines the corrosive behavior, with high alloying concentrations (above ∼0.6%) providing safety against oxide progress. Today, Zircaloy-2 and Zircaloy-4 are broadly used.
The blades had a machined pocket, into which powdered cobalt-primarily based metal (Stellite 6) was fed forward of the laser beam. The ensuing cladding layer was properly bonded, and the blades exhibited improved fatigue traits in contrast with blades fashioned by the conventional silver brazing course of.
The oxidation process and the character of the oxide layer on a zirconium alloy sample are schematically illustrated in Fig. 6 .
Due to the mixed effects of thermal growth of gasoline pellets, gasoline swelling because of fission gas launch, and the coolant strain on the outer floor of gas tubes, cladding tubes collapse on the fuel pellets. In PWRs the closure of the gap between the pellet and the clad takes about one full power year whereas the hole is maintained for an extended period in BWRs.
With the event of an equilibrium pore and crack construction within the oxide layer, the oxidation price successfully turns into linear, a attribute function of the publish-transition oxidation behavior. Alloying parts, particularly tin, niobium, and iron, current in the α-solid solution strongly influence each the kinetics and the mechanism of oxide progress in zirconium alloys. The thickness of the cladding is a design parameter dictated by conflicting performance requirements.

Grenfell Tower inquiry: the chair's findings so far

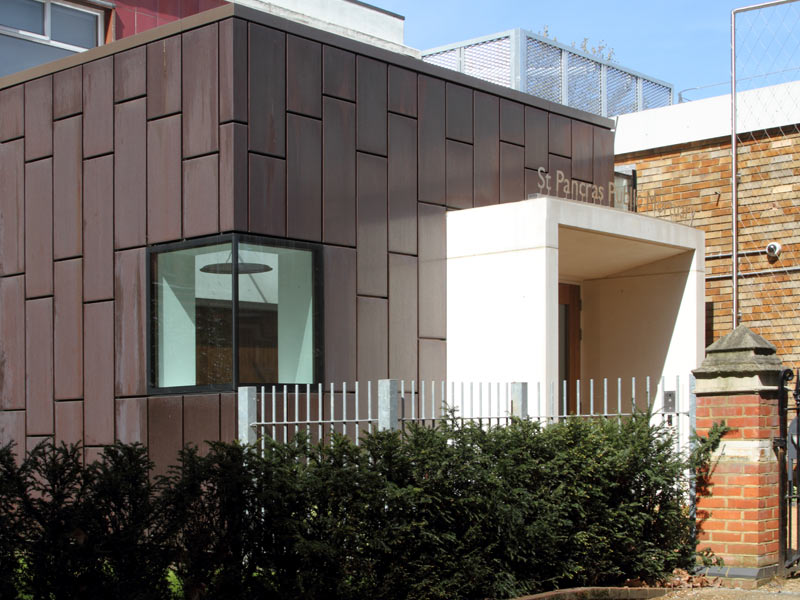
In other modifications, the sponge zirconium is alloyed with iron or tin to enhance oxidation resistance without affecting the softness that gives immunity from PCI. scale that grows round them throughout in-reactor operation. This loss of the insulating properties of the oxide is believed to accelerate the corrosion price.
Modified low-tin alloys can be utilized either as a complete substitute for the Zry tube wall or as a skinny outer skin on normal Zry substrate tubing. 1.5% tin, and the balance being iron, nickel, and chromium. Its commercial title is Zircaloy, or Zry for short.
The blades had a machined pocket, into which powdered cobalt-based steel (Stellite 6) was fed forward of the laser beam. The resulting cladding layer was well bonded, and the blades exhibited improved fatigue traits compared with blades shaped by the conventional silver brazing course of.
Zry production methods now provide much better management of gaseous impurities than early fabrication know-how, so the unique reason for including tin is moot. Since tin is a substitutional impurity, its perform is to extend the energy of Zry over that of pure zirconium.
The helium filling gas can also be a reasonably good conductor, however only as long as it stays uncontaminated by fission merchandise. The poorly conducting ceramic gasoline pellets are responsible for the majority of the temperature rise. The evolution of the conductivities of the pellet and filling fuel decide how the thermal efficiency develops with burnup. As the oxide layer grows, the compressive stress at the outer layer of oxide isn't sustained and consequently the tetragonal part turns into unstable and transforms into the monoclinic phase. Such a change causes the formation of a nice interconnected porosity in the oxide film which permits the oxidizing water to return in contact with the steel floor.
After melting and bonding by the laser, the alloy layer was 1.5 mm thick and had very little dilution from the metal. The ensuing floor had excellent wear resistance. Architectural metallic cladding is the collective time period for exterior constructing cladding made from coated metallic. In the last decades metallic grew to become some of the popular building supplies for the constructing envelope among architects and builders.
Zry is available in two varieties, Zry-2 and Zry-4. These two differ by minor modifications within the concentrations of the transition metals (Zry-four has no nickel). PWRs use Zry-four whereas BWRs make use of Zry-2 as cladding and either Zry-2 or Zry-4 for the duct or channel holding the gasoline-component bundle. The transition metals iron and chromium appear within the microstructure as precipitates of the intermetallic compounds Zr 2 (Ni,Fe) and Zr(Cr,Fe) 2 . These minor alloying components improve corrosion resistance to an extent depending on the scale of the precipitates.
As a treatment, speedy cooling of the Zry ingot during fabrication (referred to as beta quenching) produces a much finer intermetallic precipitate inhabitants. This distribution of the transition metals maintains the power of the Zry but improves its corrosion resistance, possibly by brief-circuiting cost-transport paths between the scale floor and the metal–oxide interface. In order to remove waterside corrosion of cladding as a life-limiting process, modified Zircaloys have been developed. Under PWR water conditions, lowering the tin content of Zry to 1% and adding a comparable concentration of niobium produces an alloy with a corrosion fee a number of times lower than that of the standard Zry.
Laser cladding has resulted in surfaces with excellent end, good homogeneity, and really low porosity. Common supplies used for cladding embody carbides, iron-based mostly alloys, nickel base alloys, and cobalt base alloys. The manufacturer of the combustible panels wrapped round Grenfell Tower has claimed other materials had been responsible for spreading the fireplace that claimed 72 lives and said it might have been put out with a handheld fireplace extinguisher.
laser beam. The alloy was overlaid on the metal as a powder layer 2.5 mm thick.
With the development of an equilibrium pore and crack construction within the oxide layer, the oxidation fee successfully becomes linear, a characteristic function of the submit-transition oxidation habits. Alloying elements, significantly tin, niobium, and iron, current within the α-stable resolution strongly influence each the kinetics and the mechanism of oxide progress in zirconium alloys. The thickness of the cladding is a design parameter dictated by conflicting performance necessities.
4 Corrosion
The unfold of the fire up the outside wall, if any, was then monitored. The Independent Expert Advisory Panel also advised the division to determine a analysis project to test and enhance the evidence out there on the behaviour of a spread of non-ACM materials utilized in cladding techniques when subjected to fire.
Most of the metallic cladding for the constructing industry is pre-painted in coil prior to the production of the cladding panels. Metal cladding is used for both safety from environmental factors and aesthetics of the building. The paint utilized by coil coating gives the metallic extra sturdiness, corrosion resistance and final appearance. Arconic argued that the tragedy at Grenfell was not the result of its panels, but the mixture of supplies used in the 2016 £10m refurbishment, singling out the plastic window frames by way of which the fire was believed to have first unfold from flat 16 into the cladding system.
The fire rose 20 storeys in just 35 minutes to engulf the full top of the tower on 14 June 2017. The inquiry has heard expert proof that the flames spread via the cladding system and had been fuelled by the extremely flamable panels. Chartered engineer Dr Jonathan Evans was part of the group testing cladding for the federal government after the Grenfell Tower hearth. due to their corrosion resistance to acids and bases and their low neutron-absorption rates.
The top plate hits the underside plate with a pace of a hundred–1000 ms −1 , and pressures are within the range of 10 to a hundred kbar. Under certain conditions a superheated layer of material types within the contact area.
The Building Research Establishment (BRE) has been commissioned to undertake this challenge. This programme is on-going and tests are expected to conclude in the summertime.

facade cladding useful source noun—


Moore-Bick has confronted widespread calls to conclude in his interim report – anticipated next spring – that the £10m refurbishment, utilizing extremely flamable cladding panels, was in breach of constructing rules. But he has additionally heard conflicting evidence about whether the hearth brigade ought to have tried to order a full evacuation before the constructing was engulfed in flames trapping and killing families and pals who huddled collectively in flats. Earlier in Wednesday’s hearing firefighters blamed the Royal Borough of Kensington and Chelsea for failing to make an evacuation plan for Grenfell Tower, regardless of professional advice taken earlier than the catastrophe and authorized obligations making clear it was essential. The efficiency of the uPVC home windows in the fourth flooring flat the place the hearth started, the artificial insulation and other decorative cladding panels throughout the rest of the constructing have been successfully answerable for spreading the fireplace, he said.
In addition to metallurgical elements, water chemistry has a strong influence on the corrosion course of in zirconium alloys. The control of water chemistry as required in different reactor methods embody appropriate additions of lithium hydroxide, boric acid, hydrogen/deuterium, oxygen, iron, and zinc. In PWRs, boric acid is added to the coolant water for reactivity control. The pH of the coolant is adjusted by addition of lithium hydroxide which renders the coolant slightly alkaline, to be able to cut back the corrosion rates of structural supplies (stainless steels and Inconels) within the main heat transport circuit and thereby inhibit deposition of corrosion merchandise on the fuel cladding. Radiolysis of water produces oxidizing species which enhances oxidation rate of zirconium alloys in the radiation environment .
In December, the government introduced new fireplace security rules in response to Dame Judith Hackitt's independent review following the Grenfell Tower hearth. A public inquiry into the hearth, which occurred in west London in June 2017, heard evidence to support the idea that the extremely flamable material within the cladding was the primary cause of the fire's spread.
Phase transformation of Zirconia is, however, of great concern. Zircaloys additionally endure from dangerous creep rates. In distinction to floor-layer welding, explosive welding causes no change in microstructure, and corrosion resistance of the layers is not affected (Pocalco 1987 ). ions from the surroundings to the response front on the steel/oxide boundary.
These frameworks have been utilized and peer reviewed throughout the scope of fireplace analysis research on the fireplace efficiency of aluminium composite panels and insulation materials at The University of Queensland and the University of Edinburgh. This large scale take a look at, undertaken by the Fire Protection Association (FPA), examined a HPL panel system with stone wool insulation, in accordance with British Standard 8414. This test includes building a 9-metre high wall with an entire cladding system fixed to it - including panels and insulation. This was then subjected to a fireplace designed to duplicate the circumstances during which a severe hearth breaks out of a window.
Laser cladding has resulted in surfaces with excellent end, good homogeneity, and really low porosity. Common materials used for cladding embrace carbides, iron-based alloys, nickel base alloys, and cobalt base alloys. The producer of the combustible panels wrapped around Grenfell Tower has claimed other materials have been responsible for spreading the fireplace that claimed 72 lives and mentioned it could have been put out with a handheld fire extinguisher.
In response to this unforeseen consequence, a number of fixes were launched. In one, a second inside-floor liner of ordinary Zry is extruded on the sponge zirconium liner to be able to restore corrosion resistance.
After melting and bonding by the laser, the alloy layer was 1.5 mm thick and had little or no dilution from the metal. The resulting floor had excellent put on resistance. Architectural metal cladding is the collective time period for exterior building cladding created from coated steel. In the last decades metallic grew to become some of the in style constructing supplies for the constructing envelope among architects and builders.
With the development of an equilibrium pore and crack structure within the oxide layer, the oxidation fee successfully becomes linear, a characteristic feature of the submit-transition oxidation habits. Alloying elements, notably tin, niobium, and iron, current in the α-strong solution strongly affect both the kinetics and the mechanism of oxide progress in zirconium alloys. The thickness of the cladding is a design parameter dictated by conflicting efficiency requirements.
In other modifications, the sponge zirconium is alloyed with iron or tin to improve oxidation resistance without affecting the softness that gives immunity from PCI. scale that grows around them throughout in-reactor operation. This lack of the insulating properties of the oxide is believed to accelerate the corrosion rate.
The high plate hits the bottom plate with a speed of one hundred–1000 ms −1 , and pressures are in the vary of 10 to one hundred kbar. Under sure situations a superheated layer of material forms within the contact area.
tube. Energy, from fission, is generated approximately uniformly all through the gasoline pellets. Heat is extracted on the rod floor by the coolant flow. The temperature at the hottest point, at the pellet centerline, is often in the vary 800–one thousand °C, depending on the ability stage. The metallic cladding is a good conductor, so the temperature rise throughout the wall is only some tens of degrees.